Exactly how to Recognize What is Porosity in Welding and Improve Your Strategy
Porosity in Welding: Identifying Common Issues and Implementing Best Practices for Avoidance
Porosity in welding is a pervasive problem that usually goes unnoticed up until it creates significant problems with the stability of welds. This typical issue can compromise the stamina and resilience of bonded frameworks, posturing safety dangers and causing pricey rework. By recognizing the origin creates of porosity and carrying out efficient avoidance strategies, welders can substantially enhance the high quality and dependability of their welds. In this conversation, we will certainly discover the key factors adding to porosity formation, examine its damaging impacts on weld efficiency, and go over the very best techniques that can be adopted to minimize porosity event in welding processes.
Typical Reasons For Porosity

One more frequent wrongdoer behind porosity is the visibility of pollutants on the surface of the base steel, such as oil, grease, or corrosion. When these pollutants are not effectively gotten rid of before welding, they can evaporate and end up being trapped in the weld, creating problems. Furthermore, utilizing dirty or damp filler materials can present impurities right into the weld, contributing to porosity problems. To reduce these usual causes of porosity, thorough cleaning of base steels, proper protecting gas selection, and adherence to optimal welding parameters are important methods in attaining premium, porosity-free welds.
Impact of Porosity on Weld High Quality

The presence of porosity in welding can significantly compromise the architectural integrity and mechanical residential or commercial properties of bonded joints. Porosity develops gaps within the weld steel, deteriorating its general stamina and load-bearing capacity.
Welds with high porosity levels have a tendency to exhibit lower impact strength and lowered capability to flaw plastically before fracturing. Porosity can impede the weld's capability to efficiently transfer pressures, leading to early weld failing and potential Web Site security risks in crucial structures.
Finest Practices for Porosity Prevention
To boost the structural honesty and high quality of bonded joints, what certain procedures can be carried out to lessen the incident of porosity during the welding process? Utilizing the right welding method for the particular material being welded, such as readjusting the welding angle and weapon setting, can even more avoid porosity. Normal evaluation of welds and prompt remediation of any type of issues recognized during the welding procedure are vital techniques to stop porosity and create top quality welds.
Importance of Correct Welding Methods
Executing proper welding strategies is vital in guaranteeing the structural stability and quality of bonded joints, developing upon the foundation of reliable porosity prevention actions. Welding methods directly influence the general toughness and toughness of the welded framework. One essential facet of correct welding techniques is keeping the appropriate warmth input. Excessive warm can cause raised porosity as a result of the entrapment of gases in the weld pool. Alternatively, inadequate warmth may cause insufficient combination, producing potential weak factors in the joint. Furthermore, using the appropriate welding parameters, such as voltage, current, and travel speed, is essential for achieving sound welds with minimal porosity.
Additionally, the option of welding procedure, whether it be MIG, TIG, or stick welding, need to align with the particular requirements of the job to make certain optimum outcomes. Proper cleaning and preparation of the base metal, in addition to choosing the ideal filler product, are additionally essential components of skilled welding methods. By adhering to these finest methods, welders can lessen the danger of porosity development and create high-grade, structurally sound welds.
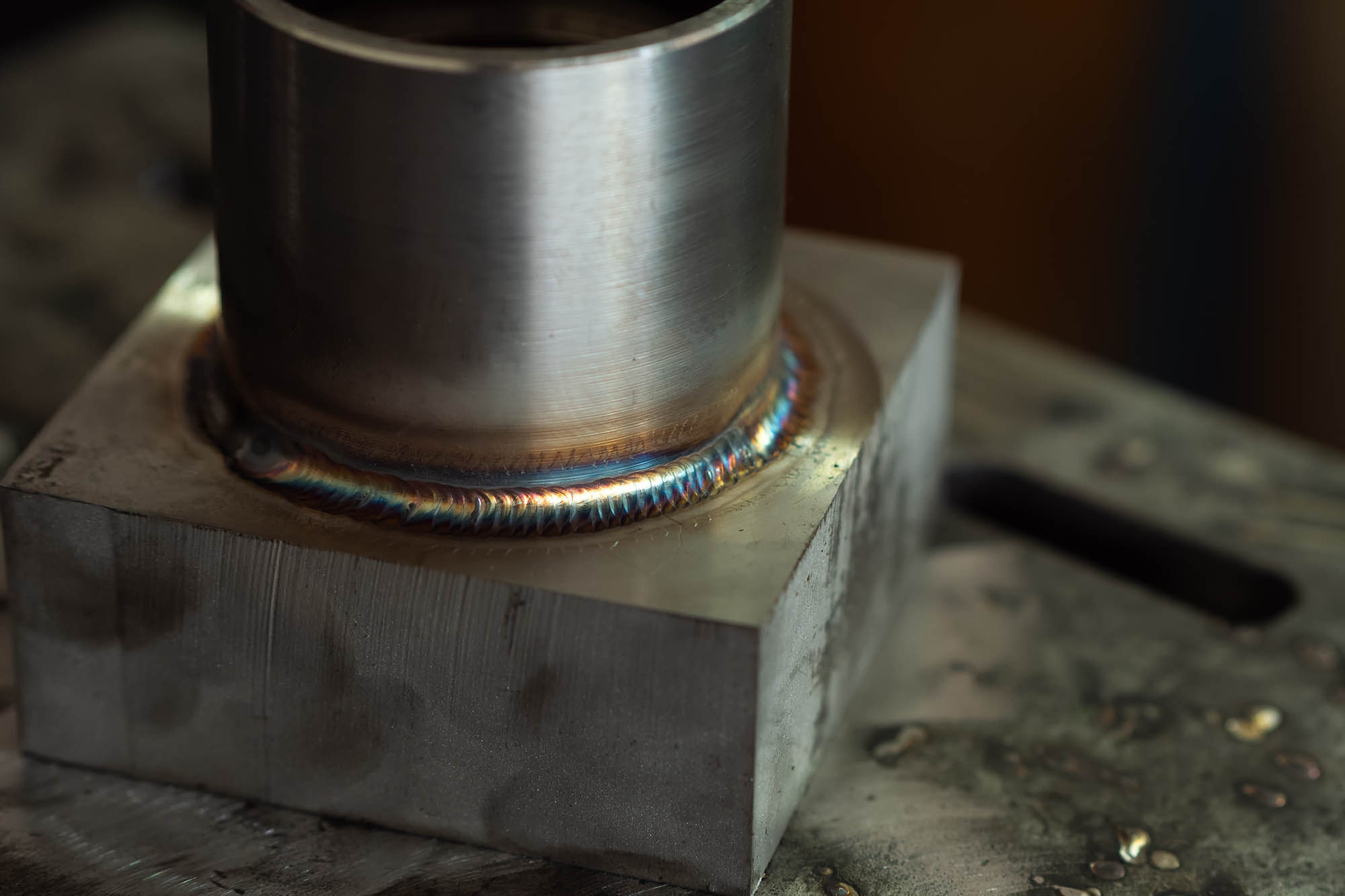
Testing and Top Quality Control Measures
Examining procedures are necessary to detect and avoid porosity in welding, making certain the stamina and sturdiness of the final item. Non-destructive screening techniques such as ultrasonic screening, radiographic testing, and visual examination are frequently used to recognize possible flaws like porosity.
Carrying out pre-weld and post-weld examinations is also critical in maintaining quality assurance criteria. Pre-weld evaluations include confirming the products, devices setups, and sanitation of the work location to protect against contamination. Post-weld assessments, on the various other hand, analyze the last weld for any kind of problems, consisting of he has a good point porosity, and verify that it fulfills defined requirements. Carrying out a thorough high quality control strategy that includes comprehensive testing procedures and inspections is critical to minimizing porosity problems visit this site right here and making sure the general quality of bonded joints.
Conclusion
In conclusion, porosity in welding can be an usual issue that impacts the quality of welds. By identifying the usual sources of porosity and executing finest methods for prevention, such as correct welding methods and testing procedures, welders can guarantee high top quality and reputable welds. It is important to prioritize avoidance approaches to minimize the incident of porosity and maintain the honesty of welded structures.